krishmrindia@gmail.com +91 7982189776
Zero Liquid Discharge (ZLD)
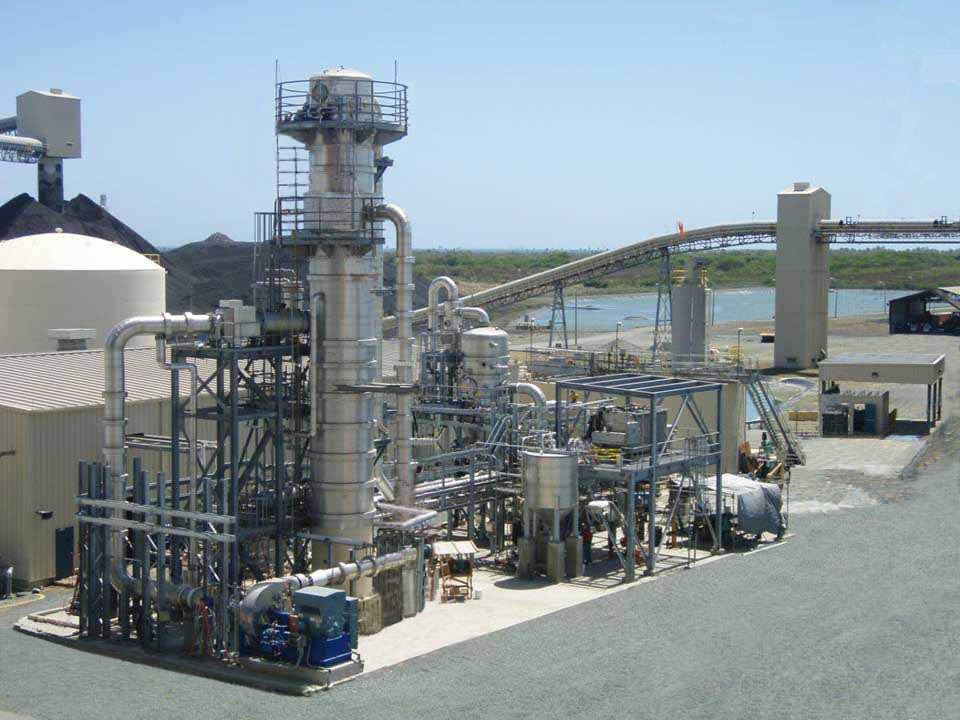
Essential of Zero Liquid Discharge (ZLD) Systems
Stricter wastewater discharge regulations have mandated industries of all sizes to update the way they run their operations for quite some time. These tightening standards not only focus on improving the quality of the water released to the environment, but also the quantities that can be discharged. For instance, the injection of wastewater deep underground has brought investigation and regulation because of concerns of increased seismic activity. This forces industrial facility operators and project developers to invest in advanced wastewater technologies that can reuse this wastewater to minimize withdrawals and limit discharges. Furthermore, activists and consumers are also increasing the pressure put on industries to be more conscious of their operating choices. In water terms, that means implementing reuse standards not only to comply with planning and permitting needs but also to avoid tapping into water sources or discharging pollutants that bring strong opposition to industry settling or expanding in many parts of the world.
Increased demands for water from municipalities, farmers and industries in arid areas are putting enormous pressure on limited water supplies which are particularly exposed to the effects of climate change. Water-intensive industries such as mining, power generation, and oil and gas extraction, need to do more with less and become more efficient with the water they take in. That means reusing what is inside the facility and reducing its freshwater intake.
Organics, volatile compounds, and constantly changing wastewater compositions can be increasingly challenging to be removed with conventional treatment programs which are also driving industry toward implement zero liquid discharge (ZLD) systems. ZLD systems are designed to take wastewater through a series of physical, chemical, and thermal technologies that produce two outputs: treated water that can be reused and, concentrated brine, which is further processed to separate salt crystals for disposal or beneficial use.
For instance, in the upstream energy sector, fracking wells require injecting large amounts of brackish water with proppants and other polymers to fracture the rocks underground. This volume of water, several times that of the oil and gas produced, requires advanced treatment to remove chemicals before recycling and completing the well. Another example is in the utilities sector when cooling tower blowdown effluents are recirculated more and more times in a closed loop. This creates more salinity and concentrations of biocides, scale-forming components, foam and corrosion inhibitors that condition the water to prevent bacteria, fouling, and corrosion. Because these chemicals may harm aquatic species and ecosystems, they need to be removed before this wastewater is discharged to the environment. More treatment steps are necessary to degrade and remove ever more challenging species.
As a result of these forces at play, innovation in the dissolved solids removal segment has brought a wave of emerging water treatment technologies: electrodyalisis reversal, reverse osmosis, forward osmosis, membrane distillation, humidification, freeze crystallization, supercritical precipitation and others. Most new approaches however are not proven at industrial scale and their operation remains more energy-intensive than that of established, commercially mature, thermal evaporation systems.
How Does ZLD Work?
In broad terms, there are two general ZLD technologies that work to remove dissolved solids and impurities: thermal and membrane processes and frequently a combination of both in a hybrid form. The rapid advance of membrane technologies over the last few decades has been nothing short of remarkable. However, thermal systems based on established, proven technologies are often considered for more robust and versatile solutions to achieve concentrations near saturation or super-saturation in both complete water recovery and near (partial) ZLD which may dispose of evaporator concentrate by injecting it deep underground.
In general, a suite of technologies can be part of a ZLD approach including ion exchange, electro-dialysis, and softening. Reverse osmosis membranes, because of their cost advantages, flexibility and compact installation are invariably used. However, hardness, silica, and other potential scaling compounds must be removed to protect their integrity. Membranes also drive and enhance the system water recovery.
This is defined as the percentage of the feed solution that may be recovered as product water. In other words, the lower the waste, the higher the water recovery. Because typical high-hardness brackish water is particularly difficult to treat under elevated pH levels, the process starts by a pre-treatment step which typically consists of softening and clarification that targets the removal of suspended solids using lime, soda ash, caustic, and other chemicals to precipitate calcium and magnesium ions in the water. The main mechanism of coagulation/flocculation happens in a mixing reactor tank with these added chemicals to promote the aggregation of suspended solids. Once the solids have formed aggregates, separation can be carried out by settling or microfiltration membranes which remove much of residual hardness, silica, and other potential scaling compounds.
The pre-concentration step is completed by reverse osmosis membranes which divide the incoming flow in two ways. On one hand, the “permeate” stream is returned to reuse or treated for further purification using ion exchange or electro-deionization, a technology that uses an electrical potential to drive physical separation and achieve a demineralized quality of below 0.5 ppm without any chemical additives. On the other hand, the “reject” stream that feeds the falling film evaporators, also called brine concentrators, where the vapor is generated by heating across a large surface area.
Thanks to their efficient heat transfer technology, evaporators produce high-purity distillate, and achieve water recovery greater than 90%. Recovered water in a brine concentrator can be recycled in many plant processes such as cooling tower, scrubber makeup, or demineralized feed water.
The pre-concentration steps achieve a key function: to reduce the volume to be thermally treated. This is important because the operation of this system requires concentrated flows to be efficient. The higher the recoveries in the pre-concentration step, the lower the costs of evaporation downstream, both capital and operational.
To complete the separation of the salts from the water, the brine produced by the evaporator feeds a crystallizer designed to further concentrate the reject volumes to the point of producing crystals. Crystallizers are designed to handle continuous crystallization of the various dissolved salts, which sometimes can be recovered as valuable by-products when equipped with solids dewatering and drying in a true zero liquid discharge system that delivers a product with about 90 percent solids content. These brine crystallizers typically are driven by live steam as in a Thermal Vapor Recompression (TVR) unit but in some cases they can use Mechanical Vapor Recompression (MVR) technology to recycle the vapor and reduce energy usage and operating costs.
Control and Automation through Digital Tools
To ease the management of operating variables in ZLD systems and maintain optimal yield, safety, quality and efficiency, digital technologies enable teams to optimize operations in multiple ways including predictive maintenance and remote monitoring of assets. Cloud-based platforms harness data from sensors and analytics to enhance control and send alarms or alert operators of critical issues through an online dashboard accessible from any device. Specialized technicians can also gain visibility remotely thanks to the power of augmented and virtual reality that saves costs in field trips to train personnel, or troubleshoot and service equipment.
Real Needs Solved with ZLD
As the high quality “distillate” or recovered water is returned as makeup water for steam generation, and the balance returned to the cooling tower, the dried solids are trucked to a landfill. Thanks to ZLD, the plant maintains optimal operation while minimizing withdrawals and protecting scarce water sources.
Oil and gas production is associated with a brackish by-product stream called produced water which is difficult to reuse in fracking operations because it contains significant quantities of dissolved solids and chloride salts.
Oil refineries, liquefied natural gas plants, and other downstream facilities have a constant demand for water to produce outputs. However, they are often located in water-stressed areas. Industrial wastewater will be treated by ultrafiltration and reverse osmosis to achieve high water recoveries for complete reuse within the plant. Thus, no liquid effluent will be discharged into the natural environment. Reverse osmosis brine treatment will be carried out by an evaporator that concentrates the brine followed by a crystallizer, a technology achieving zero liquid discharge where only salt crystals are produced for disposal.
A Proven Solution to Growing Challenges
Faced with mounting pressures from consumers growing aware of the impacts of production and its water consumption on the environment, industries are incorporating sustainability initiatives across their value chain. This is also true for water treatment systems. A zero liquid discharge approach uses technical innovation to close the loop, cut liquid waste and reuse clean water through highly efficient processes.
This helps to improve industrial productivity, protect ecosystems from harmful effluents and conserve water for the environment and communities. Many industrial plants in need of upgrading infrastructure have turned to ZLD to meet stricter local and state regulations.
Thanks to advanced brine management technologies that improve recoveries and reduce energy costs and wastewater disposal, ZLD is a solution that is up to the challenges posed by a future with rising water scarcity and growing demand for high-quality water.
KIW India Pvt. Ltd. provides industries with water treatment technologies, digital solutions, and lifecycle services that reconcile productivity and the protection of the ecosystem.
The Scope of Treated Water
Water recycling is reusing treated wastewater for beneficial purposes such as agricultural and landscape irrigation, industrial processes, toilet flushing, and replenishing a ground water basin (referred to as ground water recharge). Water recycling offers resource and financial savings. Wastewater treatment can be tailored to meet the water quality requirements of a planned reuse. Recycled water for landscape irrigation requires less treatment than recycled water for drinking water. No documented cases of human health problems due to contact with recycled water that has been treated to standards, criteria, and regulations have been reported.
Recycled Water Benefit
Recycled water can satisfy most water demands, as long as it is adequately treated to ensure water quality appropriate for the use. The Treatment and Uses chart shows types of treatment processes and suggested uses at each level of treatment. In uses where there is a greater chance of human exposure to the water, more treatment is required. As for any water source that is not properly treated, health problems could arise from drinking or being exposed to recycled water if it contains disease-causing organisms or other contaminants.
Water Recycling Can Decrease Diversion of Freshwater from Sensitive Ecosystems
Plants, wildlife, and fish depend on sufficient water flows to their habitats to live and reproduce. The lack of adequate flow, as a result of diversion for agricultural, urban, and industrial purposes, can cause deterioration of water quality and ecosystem health. People who reuse water can supplement their demands by using a reliable source of recycled water, which can free considerable amounts of water for the environment and increase flows to vital ecosystems.
Water Recycling Decreases Discharge to Sensitive Water Bodies
In some cases, the impetus for water recycling comes not from a water supply need, but from a need to eliminate or decrease wastewater discharge to the ocean, an estuary, or a stream. By avoiding the conversion of salt water marsh to brackish marsh, the habitat for two endangered species can be protected.
Water Recycling Can Reduce and Prevent Pollution
When pollutant discharges to oceans, rivers, and other water bodies are curtailed, the pollutant loadings to these bodies are decreased. Moreover, in some cases, substances that can be pollutants when discharged to a body of water can be beneficially reused for irrigation. For example, recycled water may contain higher levels of nutrients, such as nitrogen, than potable water. Application of recycled water for agricultural and landscape irrigation can provide an additional source of nutrients and lessen the need to apply synthetic fertilizers.
Recycling Water Can Save Energy
As the demand for water grows, more water is extracted, treated, and transported sometimes over great distances which can require a lot of energy. If the local source of water is ground water, the level of ground water becomes lower as more water is removed and this increases the energy required to pump the water to the surface. Recycling water on site or nearby reduces the energy needed to move water longer distances or pump water from deep within an aquifer. Tailoring water quality to a specific water use also reduces the energy needed to treat water. The water quality required to flush a toilet is less stringent than the water quality needed for drinking water and requires less energy to achieve. Using recycled water that is of lower quality for uses that don’t require high quality water saves energy and money by reducing treatment requirements.